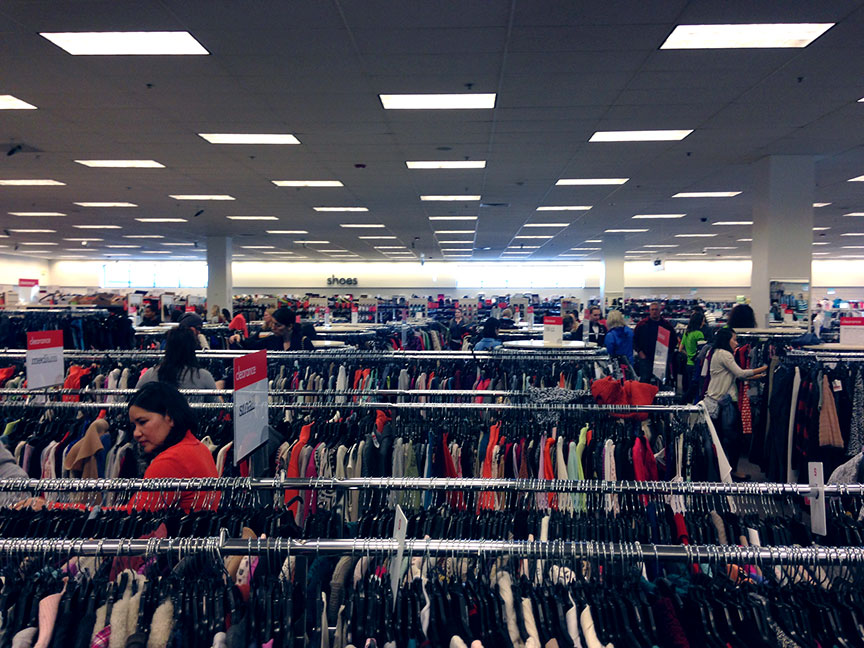
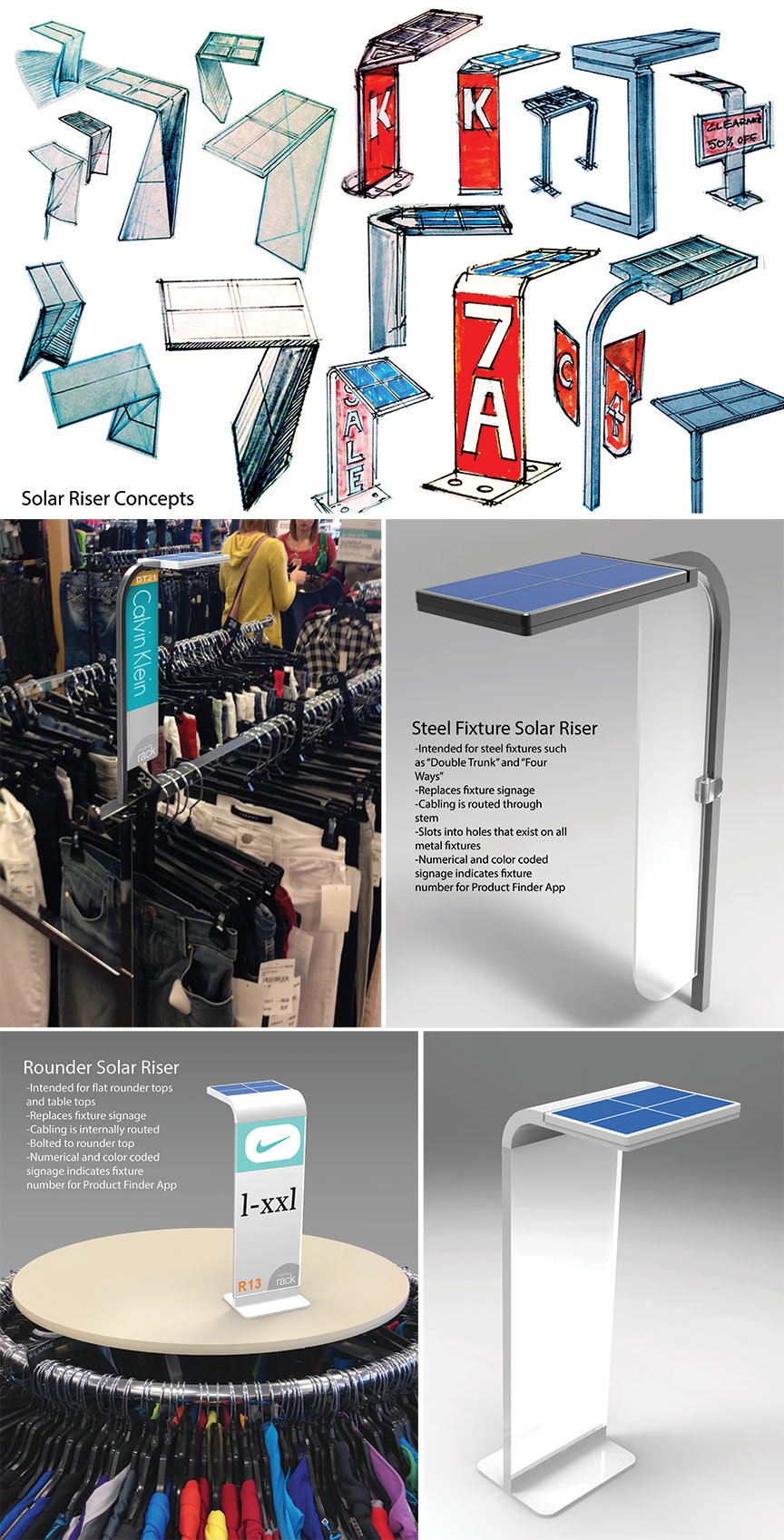

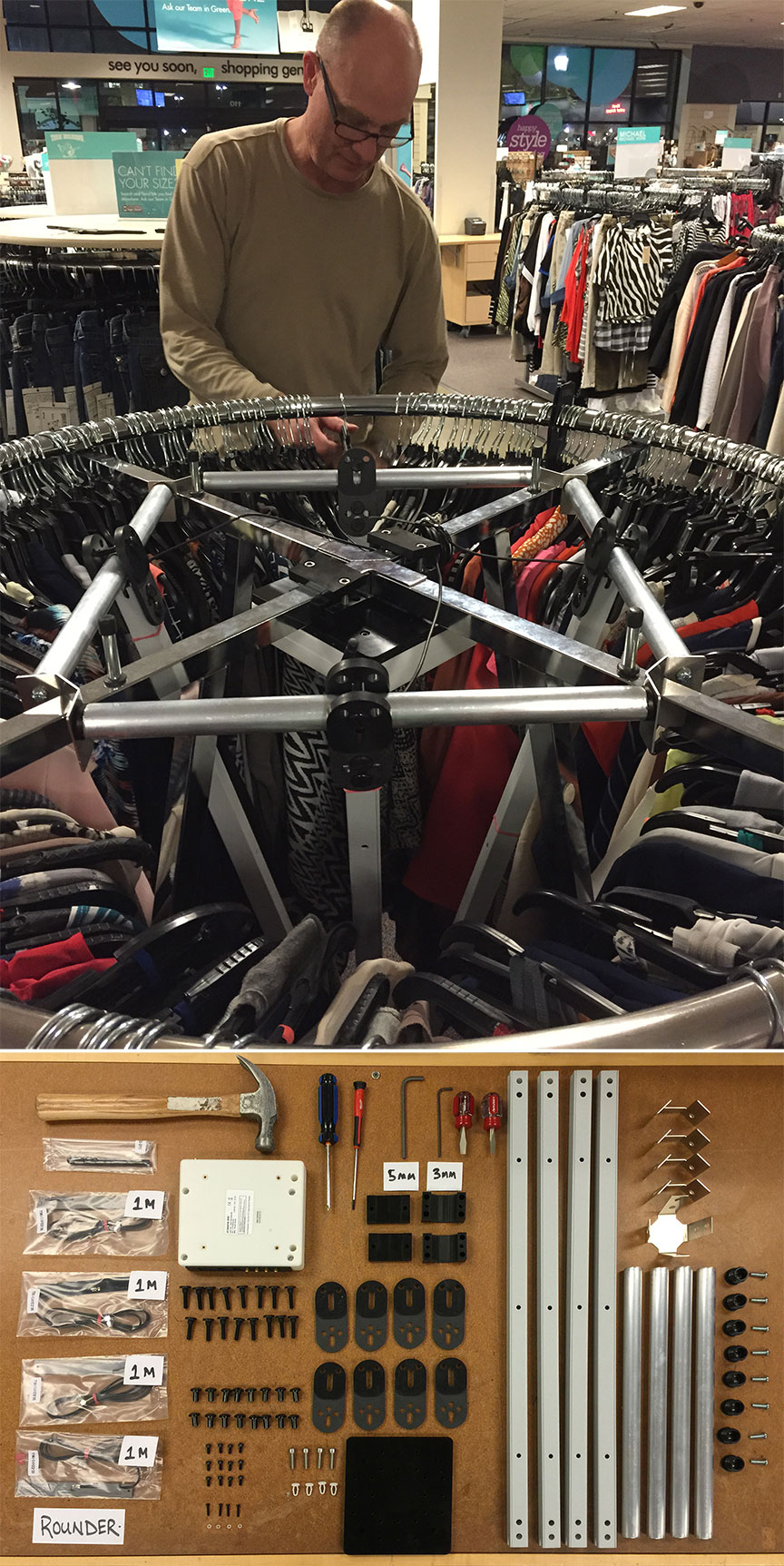
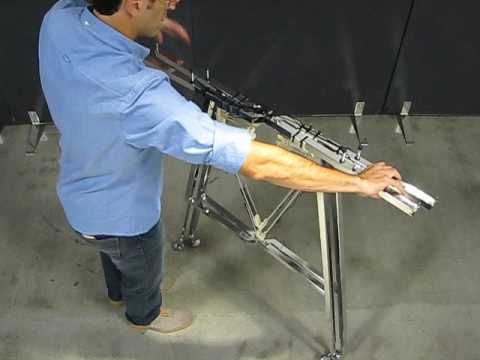
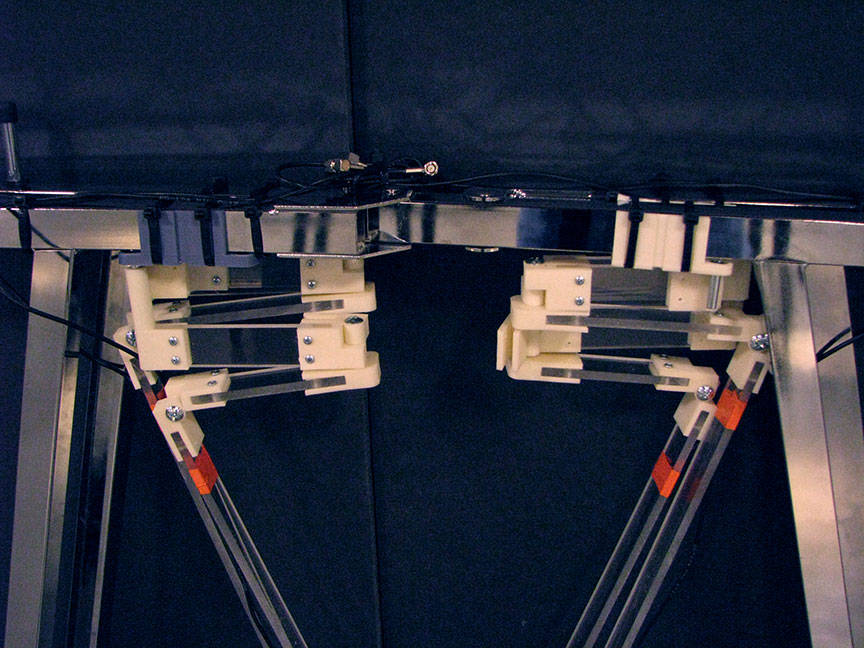
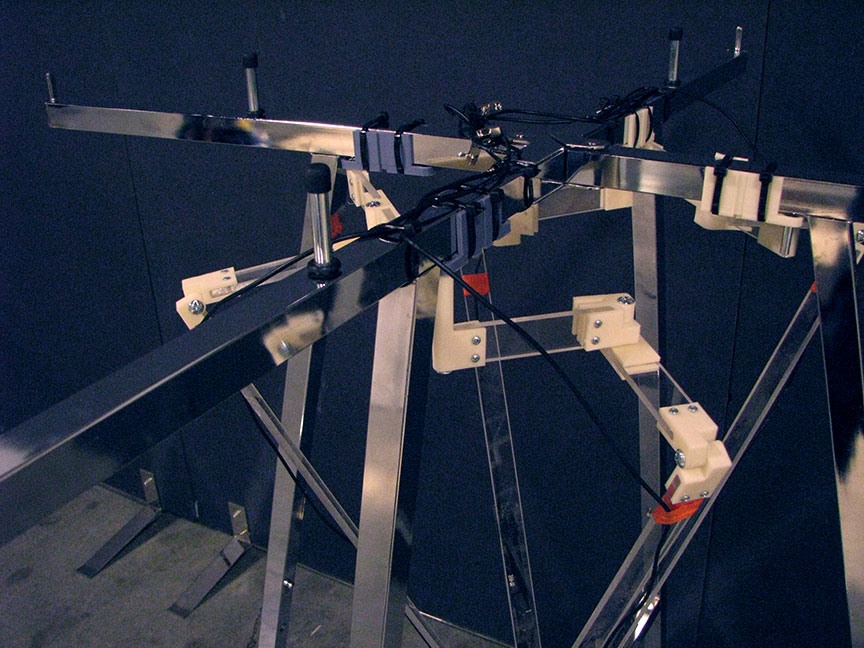
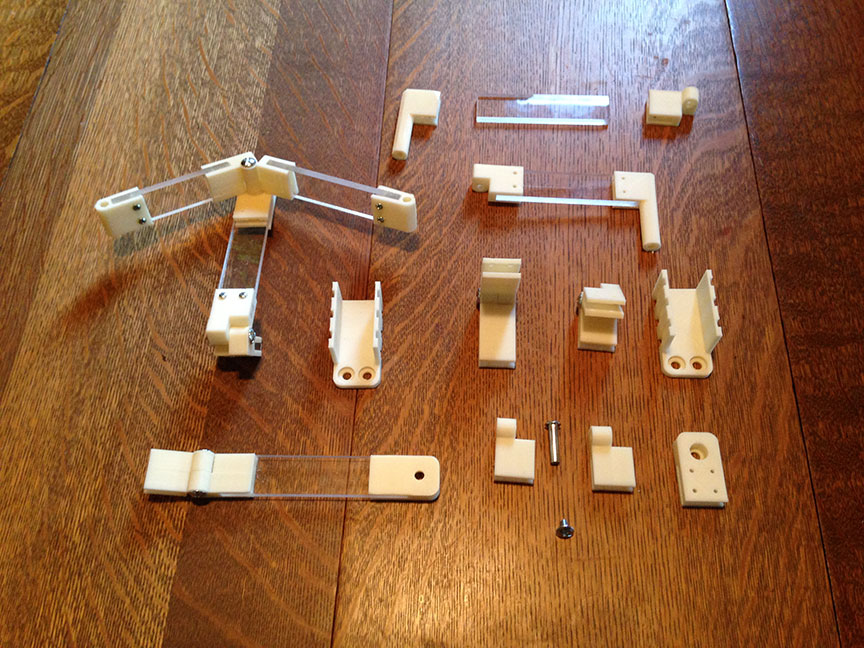
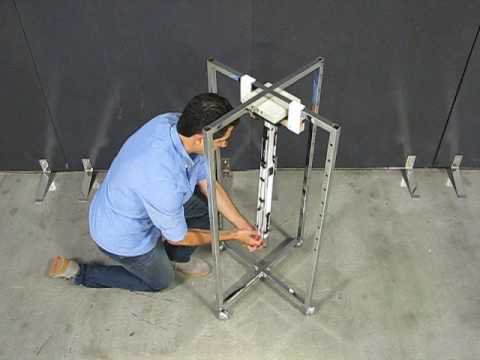
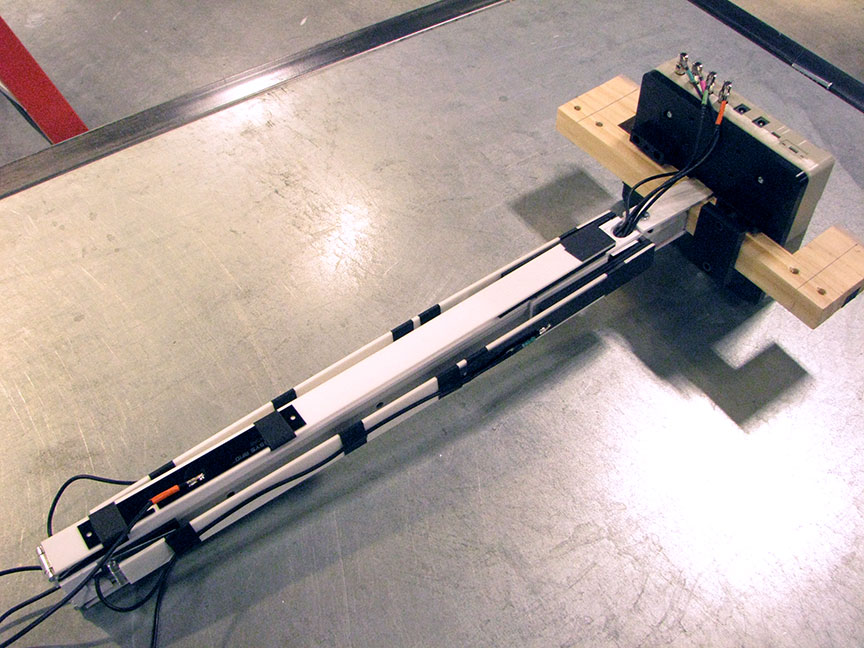
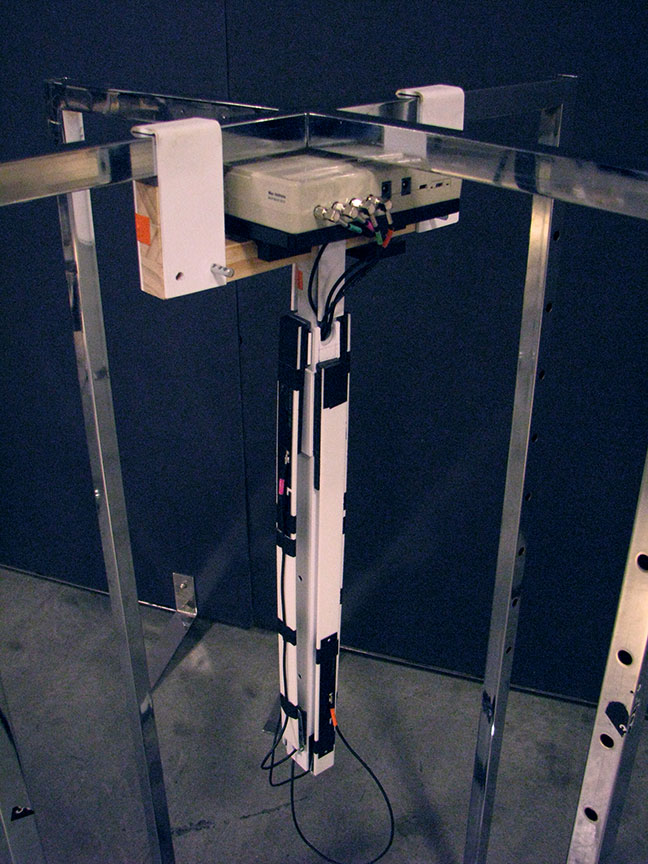
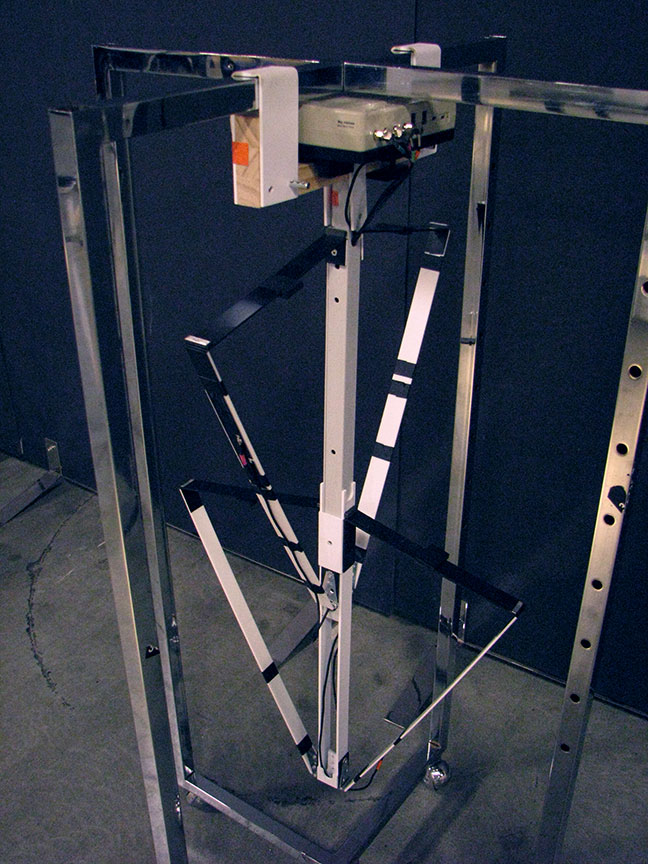
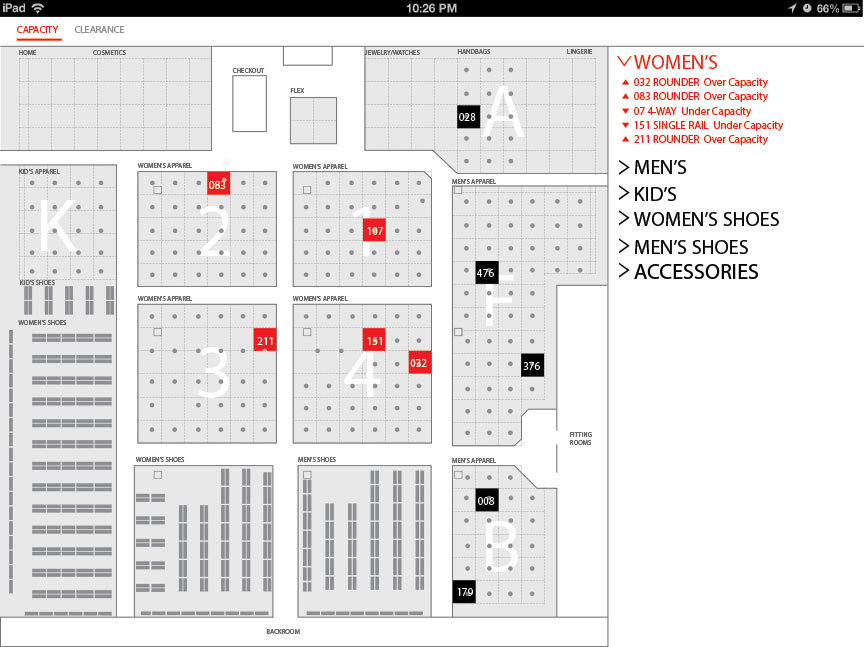
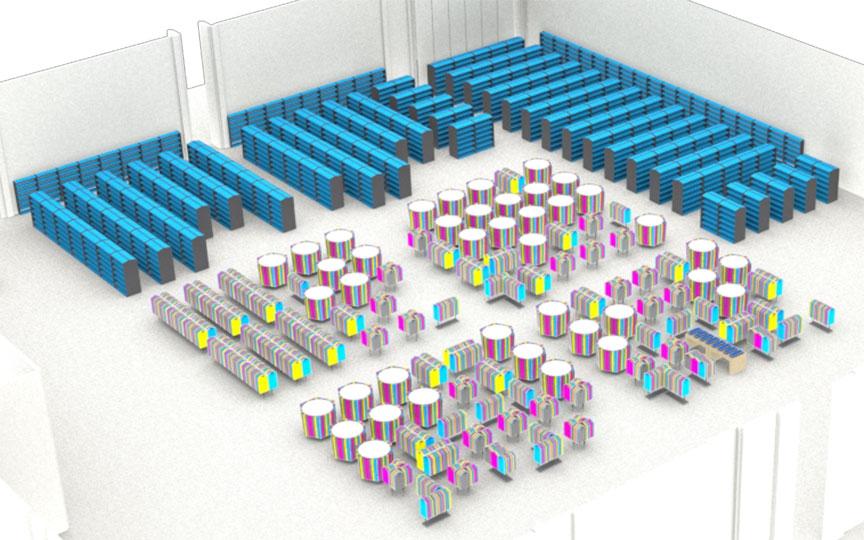
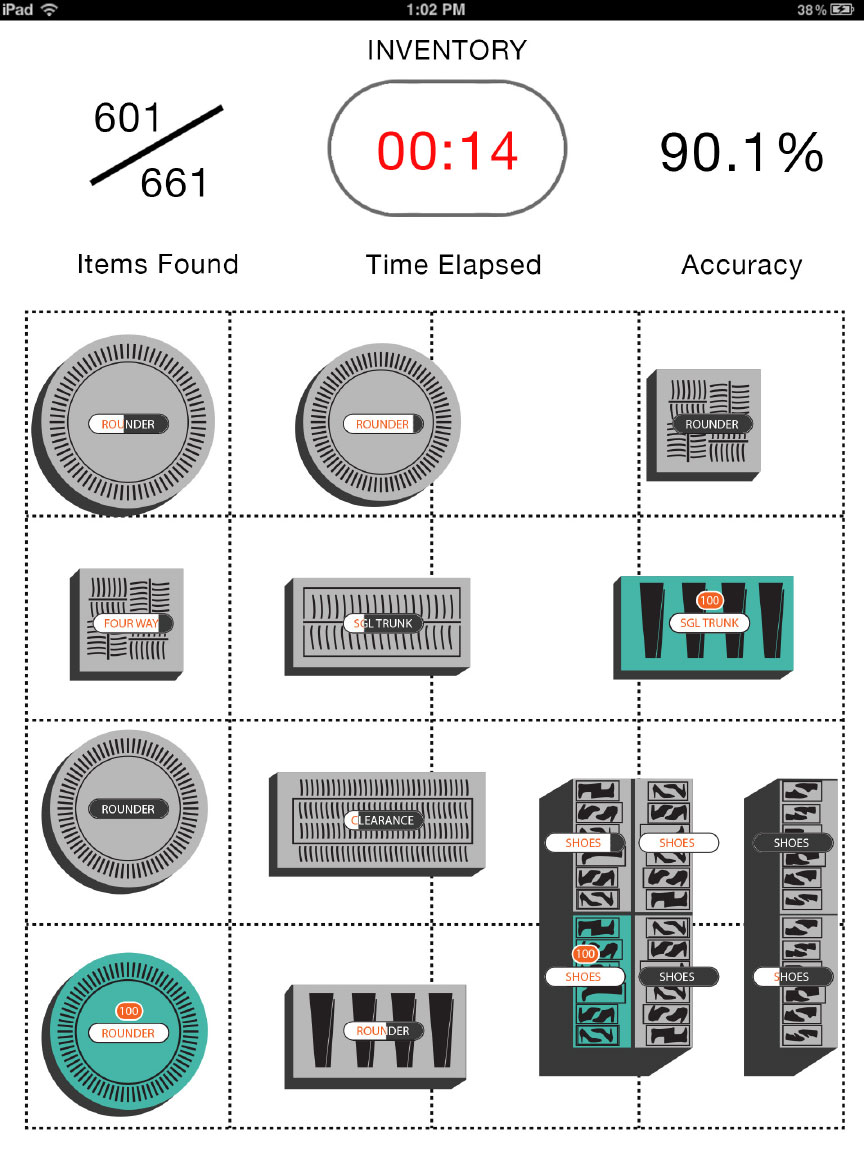
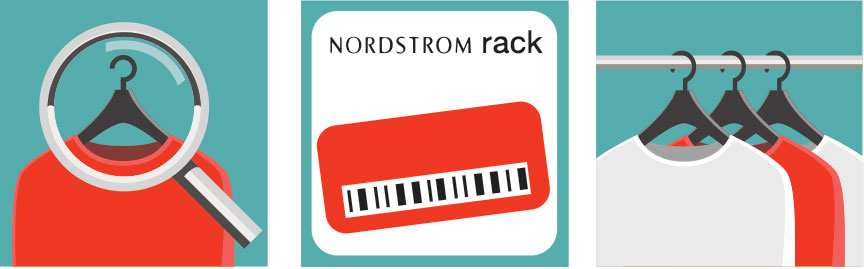
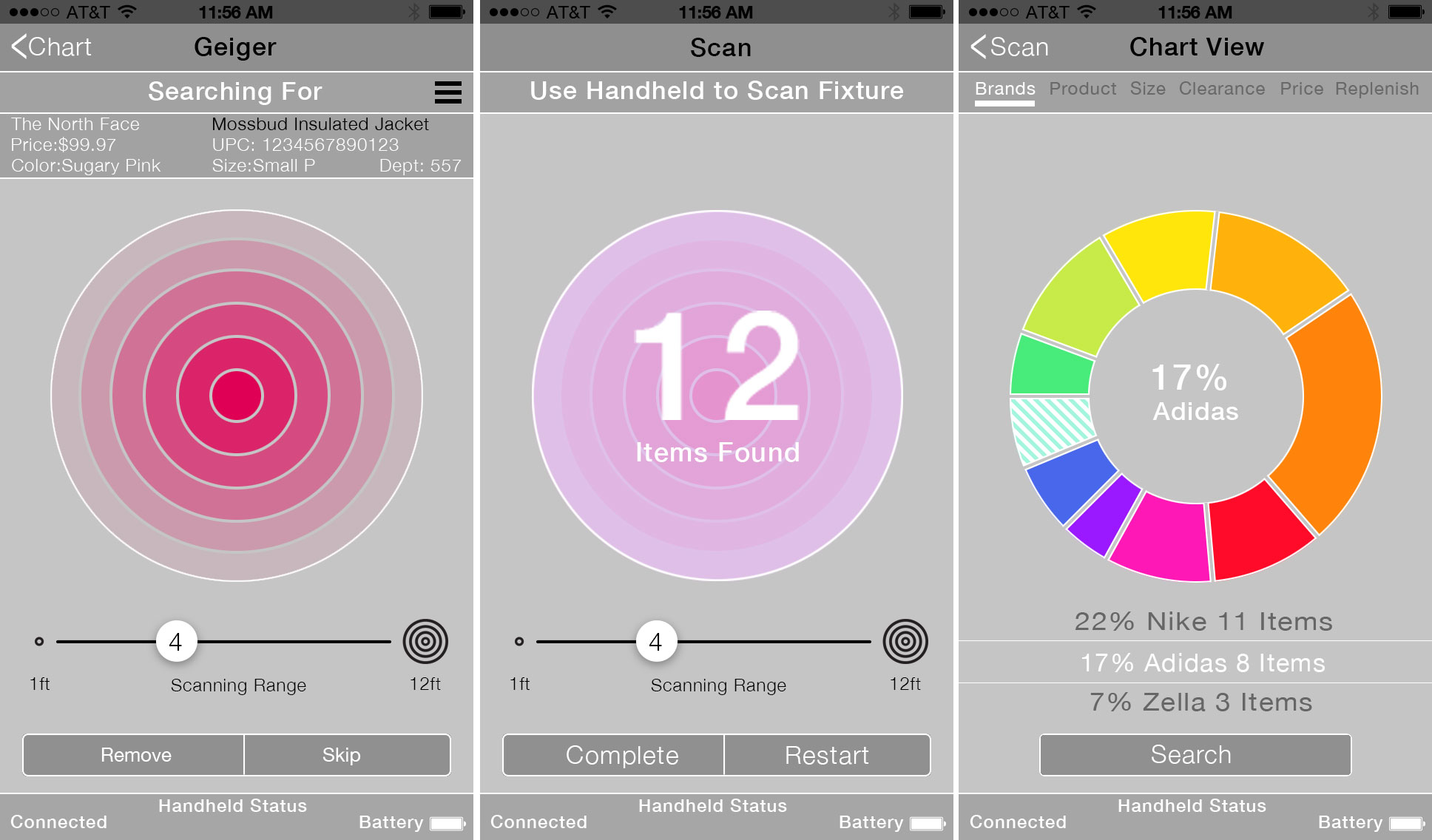
Challenge
Develop an RFID system to track the real time location of 20,000 garments across a sales floor and then supply that information to store employees to improve efficiency with product restocking, inventory, and customer service.
Synopsis
RFID is becoming a standard way to track merchandise in stores and is already integrated into many warehouses that keep products in boxes and crates. It is one of the front line technologies that is making possible the Internet of Things. Adapting this technology so that garments on a large sales floor can be precisely tracked in real time is a significant challenge beyond the traditional back of store or warehouse systems that exist. Very few garments have RFID currently and those that do have inconsistent methods of chip placement. Clothing is moved constantly around a store, whether this is from restocking, moving of fixtures, or customers trying things on and leaving the garments in dressing rooms or somewhere in the store. When a tag is attached to a flowing garment (where it can be jostled into any position and then placed in very close proximity to many other tags (as it hangs on a fixture) , read accuracy and quality drops precipitously. Compare this to a box in a warehouse where the orientation and position of the tag remain relatively static. Also compounding this problem is the amount of interference that exists on a sales floor due to hundreds of metal fixtures all scrambling good signals.
Typical retail RFID systems rely on an either an overhead reader that scans a space or handheld readers that employees use to scan for products while walking through a space, or a combination of both. These systems are very good for getting a general read of items in a store, or even providing general location of items, but for pinpointing items like clothes on a fixture where hundreds of items are likely crammed together in a few feet of space they fall short.
We worked with a strategic technical partner who developed a unique solution that would utilize inexpensive RFID hardware attached to each fixture and communicate with an overhead system to gather and expose data previously unavailable. An employee using a hand held device and app could then get very accurate information about any item in the store including it's location and which fixture it was placed on and be able to access that item in a very short amount of time.
Over the course of a year we built a functional store wide prototype, that we then tested, maintained, and improved on a daily basis. The prototype was a true mix of hardware, software, usability, and interaction that exemplifies Internet of Things requirements and challenges. As a designer I played the key role in helping to develop the hardware prototypes and interaction methods to allow store employees to use this system. One of the greatest design problems I faced was how to read the chips hanging from clothing using this fixture based system. Orientation of the hardware for optimal radio signal read and transmission was key and finding a way to do this without disrupting the clothes shopping experience or business needs of the store team was at the heart of the challenge. Furthermore, developing a method for rapid installation, removal, and storage of these components was a task placed in the design camp.
This project was rewarding example of true interdisciplinary development and ways that design could be used to help guide development of an initially strictly technical proposal.
Research
Collaborative technical research into RFID components and needs.
Worked with senior engineers and scientists to understand layout and orientation of RFID antennas to gain best interaction with RFID chips.
Spent countless hours on the floor of Nordstrom Rack observing customer interaction with product and fixtures. Observed and interviewed employees about daily routines around stocking and replenishment of fixtures, as well as their methods of customer interaction. I dove deep into this including time spent training and operating the cash wrap to understand the practical needs and behavior of employees and customers.
Design
Early involvement taking a strictly engineering project and helping to guide it into something that was ready for employee and customer interaction. I made a detailed audit of all of the fixtures in a Rack store and helped to create a prototype that would attach to this range of fixtures.
Design, fabrication, and installation of prototypes, conceptual illustrations, small scale production hardware, and interaction concepts and content for digital app.
Implementation
Worked with overseas engineering team to build and roll out a small production scale modular prototype that was then implemented into a Rack store.
Spent multiple weeks preparing, organizing, installing, and maintaining new hardware components as well as gaining learning as to impact on the store and making on the fly changes as necessary
Testing
Worked in conjunction with internal and external engineering and analyst teams to test and maintain rfid readers on a daily basis.
Production
After the results of our 3 months test, I took the results to develop prototypes for an antenna system that could be installed and uninstalled in seconds (as opposed to 20-30 minutes for our store wide test prototypes). I designed and fabricated multiple working prototypes that were used to inform and guide our engineering team as they moved forward on production concepts.
Presentation
Throughout the project I was involved in presenting to Nordstrom staff from floor sales to senior executive level employees. I Worked with multiple internal teams to gain alignment on goals and procedures to keep customer impact during test period to a minimum and pave the way for future partnerships across the company.